Boost Electronics Manufacturing Quality: Does In-House Nitrogen Generation Hold the Key?
Nitrogen, valued for its exceptional purity levels of up to 99.9995%, plays a pivotal role in Electronics Manufacturing. Its versatile applications in the Electronics industry span crucial processes such as Wave Soldering, Selective Soldering, Reflow Soldering, Blanketing, and Dry Box Storage, among others. Among these, Soldering stands out as the most prevalent application in the Electronics sector, consistently requiring top-notch Nitrogen quality with an oxygen content as low as 10 ppm. Soldering, a fundamental process in Electronics Manufacturing, involves joining two distinct metal types using an alloy known as solder. Historically, solder was primarily composed of Tin (63%) and Lead (37%). However, with the industry's shift towards environmental sustainability, there has been significant adoption of Lead-Free soldering approaches as Electronics Manufacturing continues to evolve. This shift underscores the critical importance of maintaining stringent standards for Nitrogen quality in modern electronics production.
The transition to the Lead-Free approach necessitates the use of solder alloys containing costly metals such as silver, and copper blended with tin to ensure the production of high-quality PCB assemblies. In today's electronics industry landscape, SAC305 and SN100C solders have emerged as the most prevalent choices. However, given the associated costs, the industry demands impeccable quality, making the presence of dross unacceptable in this competitive environment. Oxidation represents a significant factor contributing to elevated dross levels, emphasizing the need for an inert atmosphere to counter this issue. Nitrogen, with its inert properties, presents an ideal environment for soldering, acting as a crucial element in mitigating oxidation-related challenges and ensuring the flawless production of electronic components.
Nitrogen Gas Generation and Soldering
The diverse soldering techniques—Wave Soldering, Selective Soldering, and Reflow Soldering—impose varying Nitrogen requirements, each tailored to their specific processes. Take, for instance, Wave Soldering, which employs an 18” nozzle and demands nearly ten times more Nitrogen than its Selective Soldering counterpart. Recognized Selective soldering machines like Kurtz ERSA exhibit a minimalistic requirement, utilizing only 1.5 m3/hr of Nitrogen gas at a purity of 99.999% per pot. Notably, the nitrogen requirement typically follows a linear progression with an increase in pots; a two-pot soldering machine, for example, necessitates a consistent flow of 3 m3/hr of Nitrogen. It's worth highlighting the importance of consulting with the manufacturer to ascertain specific nitrogen requirements, encompassing factors like flow, pressure, and purity, to ensure optimal performance and efficiency.
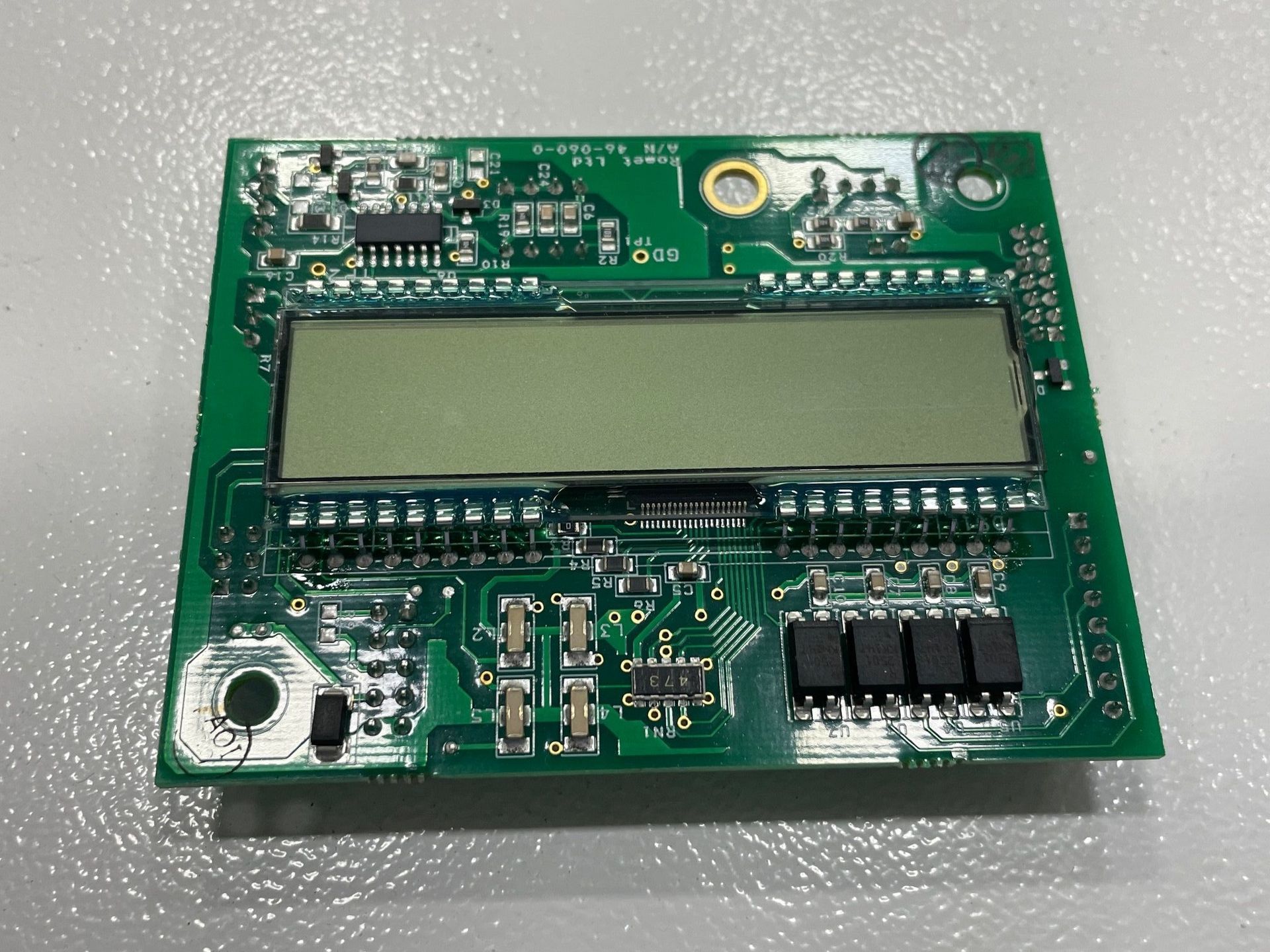
Advantages of In-House Nitrogen Generation
While Nitrogen proves indispensable in Electronics manufacturing, it comes at a significant cost, with delivered Nitrogen tailored for the industry averaging around 80 cents per m3. Despite the prevalence of this essential gas, many electronics manufacturers continue to adhere to traditional methods for meeting their Nitrogen requirements—relying on cylinders, dewars, tanker deliveries, among others. However, a notable shift is underway, with a growing number of manufacturers opting for an in-house Nitrogen Generation approach. This strategic move holds several advantages, as Nitrogen Generators offer users a range of benefits, including:
Low Cost
Opting for in-house Nitrogen Generation like the Peak i-Flow Nitrogen Generator presents a cost-effective solution. Producing Nitrogen with a purity of 99.999% can be achieved at approximately 8 cents per m3. This translates to a remarkable reduction, making it only 1/10th of the cost compared to purchasing Nitrogen from a gas company. The substantial cost savings become a compelling factor for electronics manufacturers looking to enhance their operational efficiency and bottom line.
Quick ROI
Investing in an in-house Nitrogen Generator proves to be a financially savvy decision, with the typical Return on Investment (ROI) ranging from 8 to 12 months. This swift return underscores the economic viability of such a system. Moreover, considering the longevity of a well-maintained Nitrogen Generator, often exceeding 15 years, the practical outcome is like a virtually free supply of Nitrogen for over 14 years. This not only enhances the financial attractiveness of the investment but also contributes significantly to long-term cost savings and operational stability for electronics manufacturers.
Stop Waiting & Coordinating Nitrogen Deliveries
The dependence on third-party suppliers for Nitrogen delivery often introduces challenges in coordination, leading to potential delays and disruptions. Electronics manufacturing processes can be particularly sensitive to such interruptions, with the risk of running out of Nitrogen or the need for constant vigilance over the remaining gas in cylinders or dewars. The absence of Nitrogen poses a significant threat, exposing soldering processes to an oxygen-rich environment and increasing the likelihood of oxidation. Whether the Nitrogen requirement is intermittent or continuous, an in-house Nitrogen Generator eliminates these coordination challenges by providing a seamless and on-demand Nitrogen supply, ensuring a consistent and reliable source for electronics manufacturing operations.
Expandability
In the era of Industry 4.0, where digitization is driving exponential growth in the electronics sector, manufacturers are continually expanding their capacities and integrating more soldering machines. Addressing the need for scalable solutions, the installation of a modular and expandable Nitrogen Generator emerges as the optimal choice. This innovative approach offers the flexibility to increase capacity within minutes, akin to assembling building blocks. Imagine doubling the capacity of a Nitrogen Generation system by seamlessly adding two banks, as illustrated in the accompanying images. This adaptability positions manufacturers to meet the ever-growing demands of the electronics industry efficiently and stay ahead in the dynamic landscape of technological advancement.
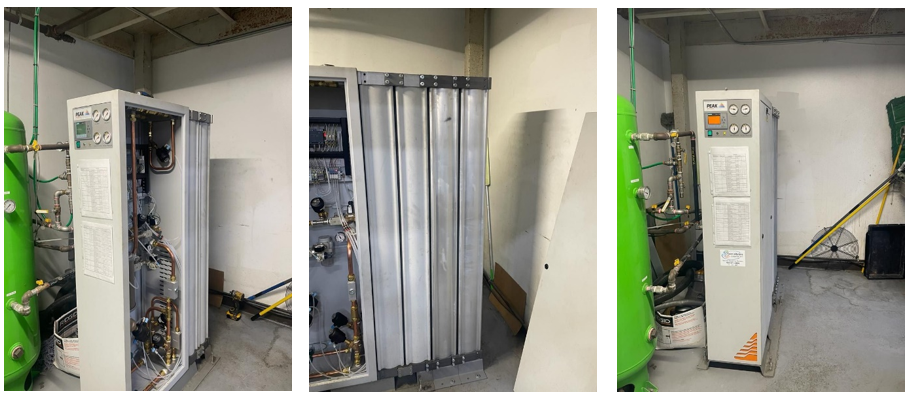
Eliminate Inflation
In light of the Producer Price Index, the Industrial Nitrogen Gas price has experienced a substantial surge of nearly 50% since January 2020. In contrast, extracting Nitrogen from the atmosphere, a process inherent in on-site generation, remains unaffected by external price fluctuations. Furthermore, the hydro cost for Nitrogen production has seen only modest increases, typically in the low single-digit percentage points. This stark contrast emphasizes the financial prudence of becoming independent and assuming control over Nitrogen Gas production. Choosing an in-house Nitrogen Generator emerges as a far more cost-effective and efficient approach to meet Nitrogen requirements, shielding manufacturers from the impact of inflation on industrial gas prices.
Worried about the Gas Quality
The adage "You can't improve what you don't measure" holds true, especially when it comes to delivered gas. In conventional scenarios, customers lack the means to check the purity of delivered Nitrogen gas without special tools. In stark contrast, Nitrogen Generators are equipped with an oxygen PPM sensor, enabling users to precisely measure the purity of Nitrogen produced. While for many Nitrogen Generator suppliers this feature may be optional, Peak i-Flow Nitrogen Generators set a standard by including the nitrogen purity sensor as a fundamental component. This eliminates guesswork, providing users with a reliable and standardized method to ensure Nitrogen purity, offering peace of mind in every production cycle.
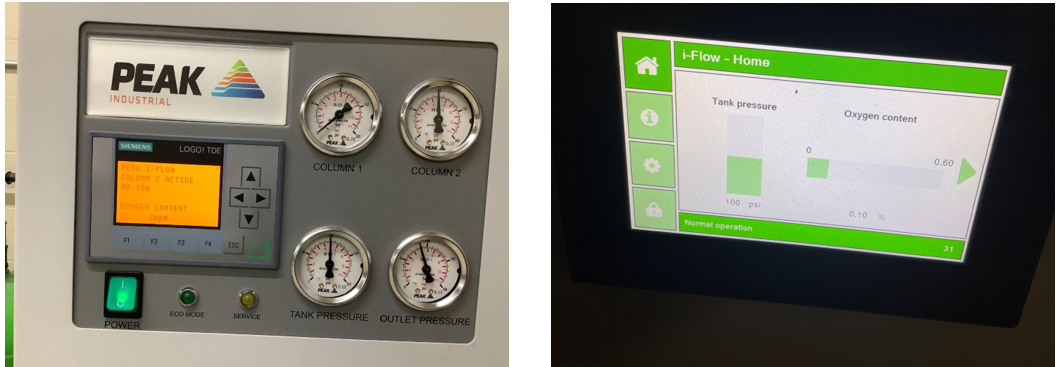
No More Freezing Lines
One common grievance among users involves the freezing of Nitrogen lines in Dewars, attributed primarily to two factors. Firstly, the extremely low temperature of Liquid Nitrogen stored in the Dewar is around -200 °C. Secondly, the fluctuating demand for Nitrogen gas worsens this issue. In contrast, the gas generated by a Nitrogen Generator emerges at ambient temperature, eliminating the risk of freezing lines. This distinction underscores a key advantage of on-site Nitrogen generation, ensuring a consistent and unconstrained supply of Nitrogen without the challenges posed by freezing lines, a common concern associated with conventional Dewar systems.
Low/No Maintenance Cost
In the current era, Nitrogen Generators have evolved to require minimal maintenance. Take, for instance, the Peak i-Flow Nitrogen generators, which typically necessitate only one service in a period. Moreover, this service is primarily associated with routine tasks such as changing the filters and mufflers. This streamlined maintenance requirement not only reduces downtime but also contributes to low or even negligible maintenance costs. Embracing modern Nitrogen Generators translates into a hassle-free and cost-effective solution, aligning with the efficiency demands of contemporary electronics manufacturing.
Environment Friendly
A significant environmental benefit of adopting an in-house Nitrogen Generation approach lies in the substantial reduction of carbon footprint. Traditional reliance on delivered Nitrogen involves frequent truck deliveries, contributing to emissions and transportation-related environmental impacts. With the shift to on-site Nitrogen Generation, there is a notable elimination of the need for these truck deliveries. This not only reduces the carbon emissions associated with transportation but also aligns with sustainable practices by minimizing the environmental impact of logistics in the Electronics Manufacturing supply chain. As industries increasingly focus on eco-friendly solutions, the transition to in-house Nitrogen Generation emerges as a pivotal step in mitigating the environmental impact of manufacturing processes.
Making the Move to InHouse Nitrogen in Electronics Manufacturing
In summary, Onsite Nitrogen Generation Solutions revolutionize Electronics Manufacturing, ensuring high-quality PCB assemblies crucial for Industry 4.0 growth. The traditional reliance on delivered Nitrogen presents challenges, from escalating costs to environmental impact. Adopting an in-house Nitrogen Generator, like the Peak i-Flow, offers cost efficiency, rapid ROI, scalability, and a consistent, on-demand supply. Beyond financial benefits, it reduces the carbon footprint by eliminating truck deliveries. This strategic move not only addresses current challenges but also positions manufacturers for long-term success in a competitive and environmentally conscious industry.
Share This Article With Your Network
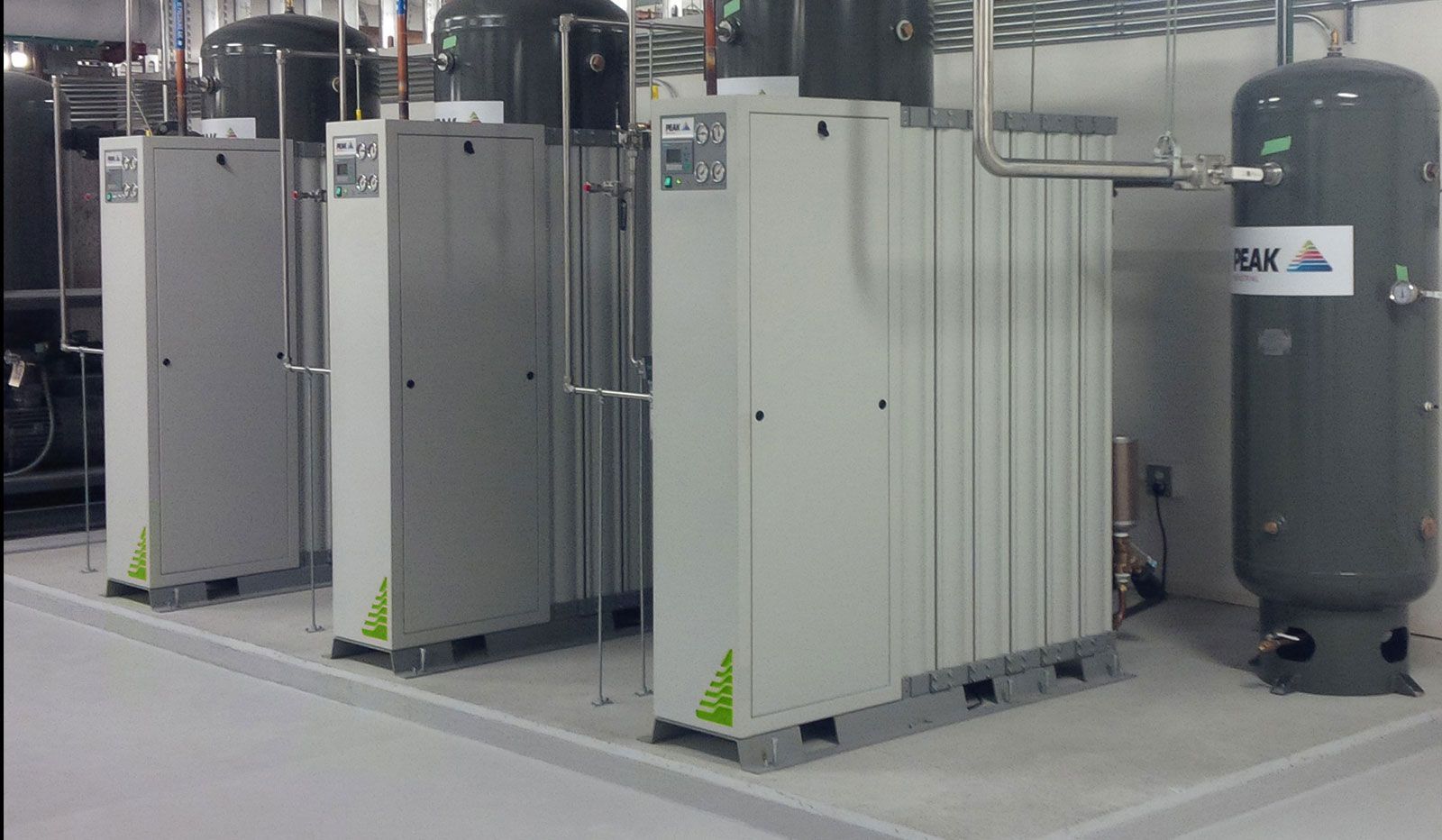